Printed Circuit Board Assembly Equipment
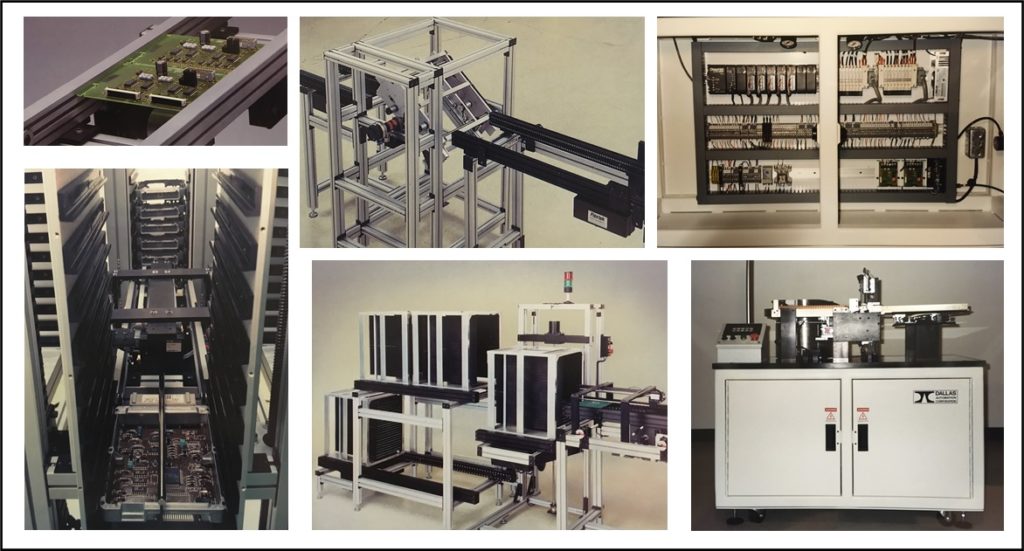
Designed motion control systems for robotic printed circuit board (PCB) assembly. Board handlers used a custom 8052 microcontroller with multiple axis stepper and servo control with 0.001” positioning accuracy. The equipment included PCB conveyors, handling modules, insertion modules, and storage units. Semiconductor handlers used Automation Direct PLC systems. This equipment tested each semiconductor for functionality before sorting and orientation for insertion into the target PCB.
Industrial Equipment
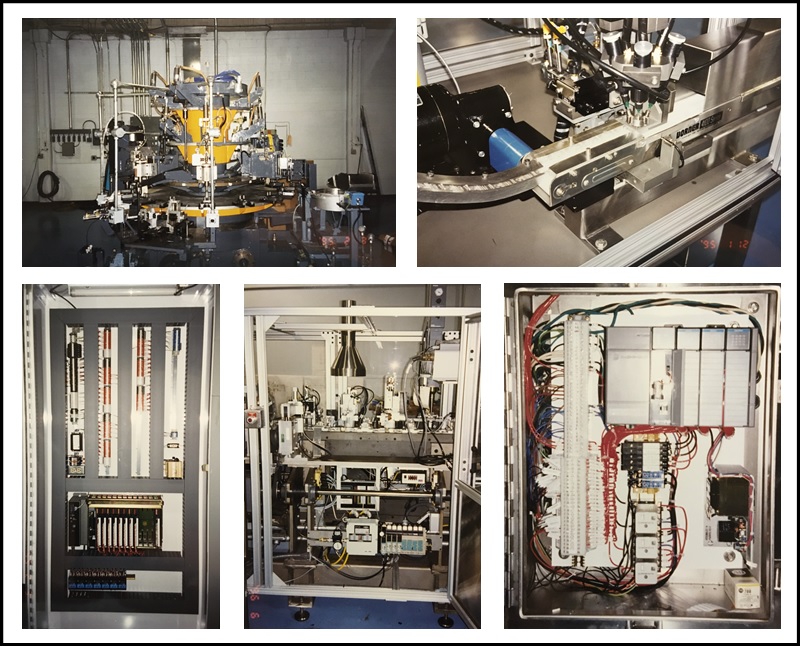
Developed and designed instrumentation and control systems for industrial and military applications. These systems utilized a large variety of control and electromechanical components, including machine vision, motion control, and Fanuc robot cells. Applications included ordnance and airbag assembly machines designed for hazardous materials operations. Manufacturing applications included process control analyses, statistical measurements, and quality control implementation. The machines used programmable logic controllers (SLC-5, PLC-5 – Allen-Bradley – Rockwell Automation). Systems were designed for electronics equipment assembly, printing press automation, air compressor testing, hydraulic drilling machines, high-speed conveyor systems for airbag propellant, airbag module assembly, ordnance assembly, and inspection.
Biomedical Manufacturing Equipment
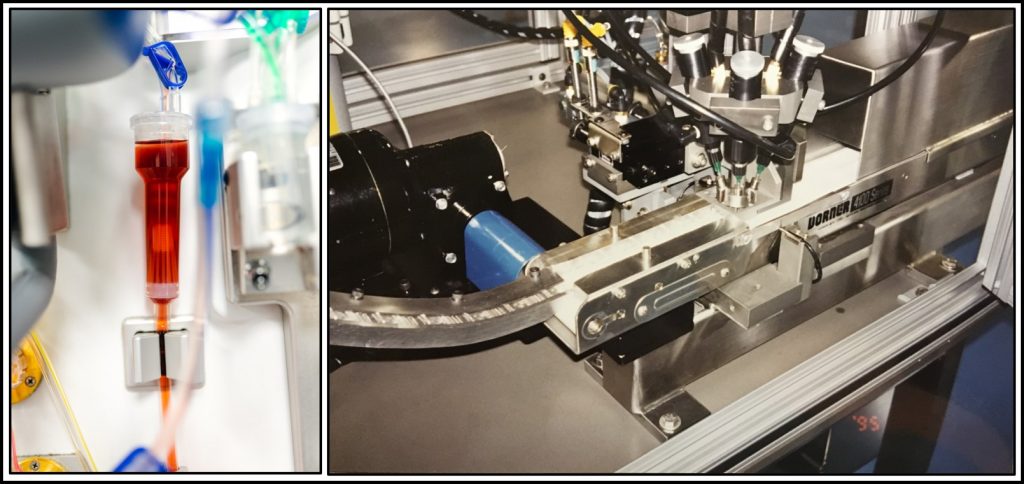
Developed and designed instrumentation and control systems for biomedical manufacturing equipment. The machines used programmable logic controllers (SLC-5, PLC-5 – Allen-Bradley – Rockwell Automation). Manufacturing applications included process control analyses, statistical measurements, and quality control implementation. Systems were built for manufacturing blood pressure sensors, surgical manifolds for delivery of fluids and gases, fluid collection systems, eyeglass lens handling and packaging, medical fiber-optic assemblies, and lens coating process equipment.
Optical Spin-Coat Process
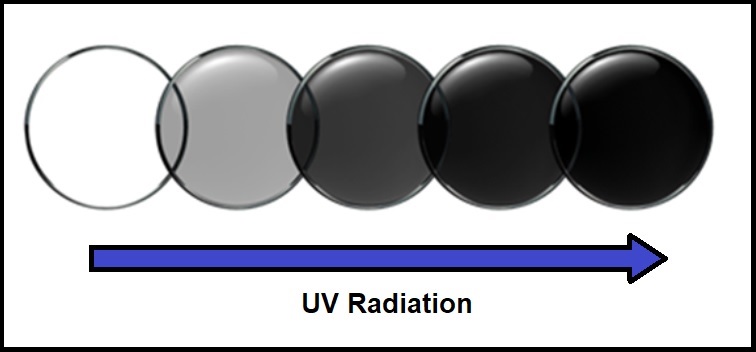
Developed the high-speed manufacturing process for the deposition of photochromic dye onto Transitions Optical lenses which activate when exposed to UV radiation. Designed the control system hardware for rotary index machines that applied the photochromic dye, spun the lenses at a precise angular velocity profile, and processed the coated lenses. These manufacturing machines included precision motion control (Bodine Electric Co.), custom dispensing systems, pneumatic and vacuum systems, and a Class-100 cleanroom shroud. The machines used programmable logic controllers (PLC-5 – Allen-Bradley – Rockwell Automation) with analog control of the motion parameters.
High-Speed Force Treadmill
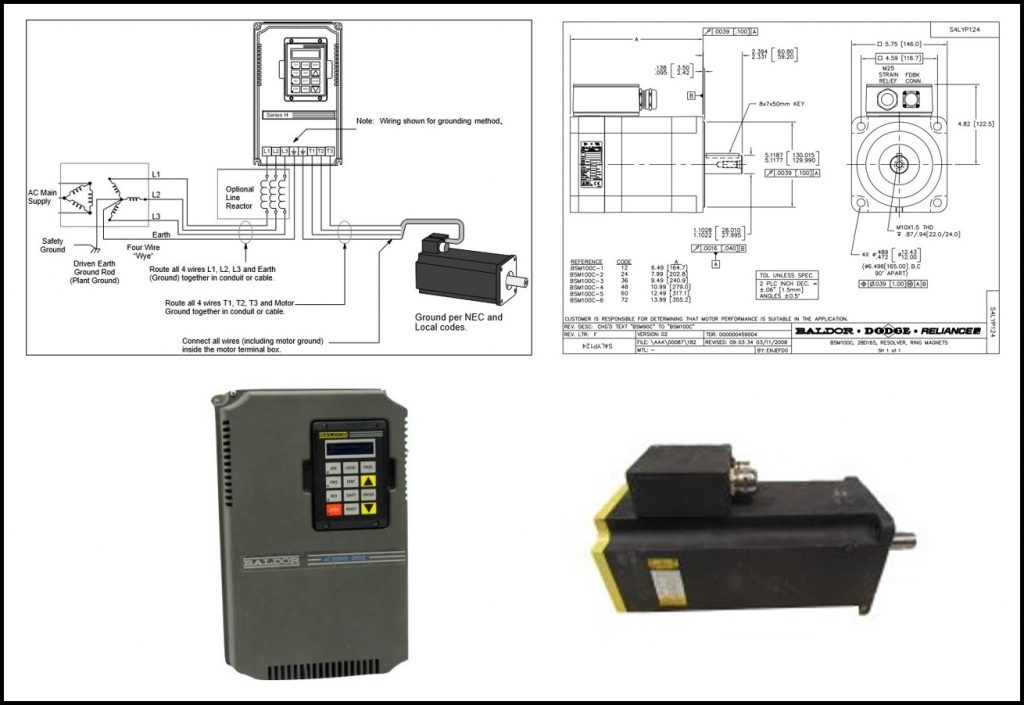
Updated the control system on a custom AMTI force treadmill. The treadmill used a direct drive Baldor BSM100C-4ATSAA custom high-speed servo motor and a Baldor SD23H2A22-E stock servo controller. The servo system velocity control loop operated at 30 Hz. Servo tuning parameters were updated and an Omega DP24-E process meter was installed to monitor speed. The speed display was calibrated using an NIST traceable Shimpo DT-207L-S12 digital laser tachometer directly on the belt. The treadmill was capable of speeds of over 20 meters per second and had sufficient power and response time to have negligible belt speed fluctuations with loads up to 300 pounds.