Handbook of Magnetic Measurements
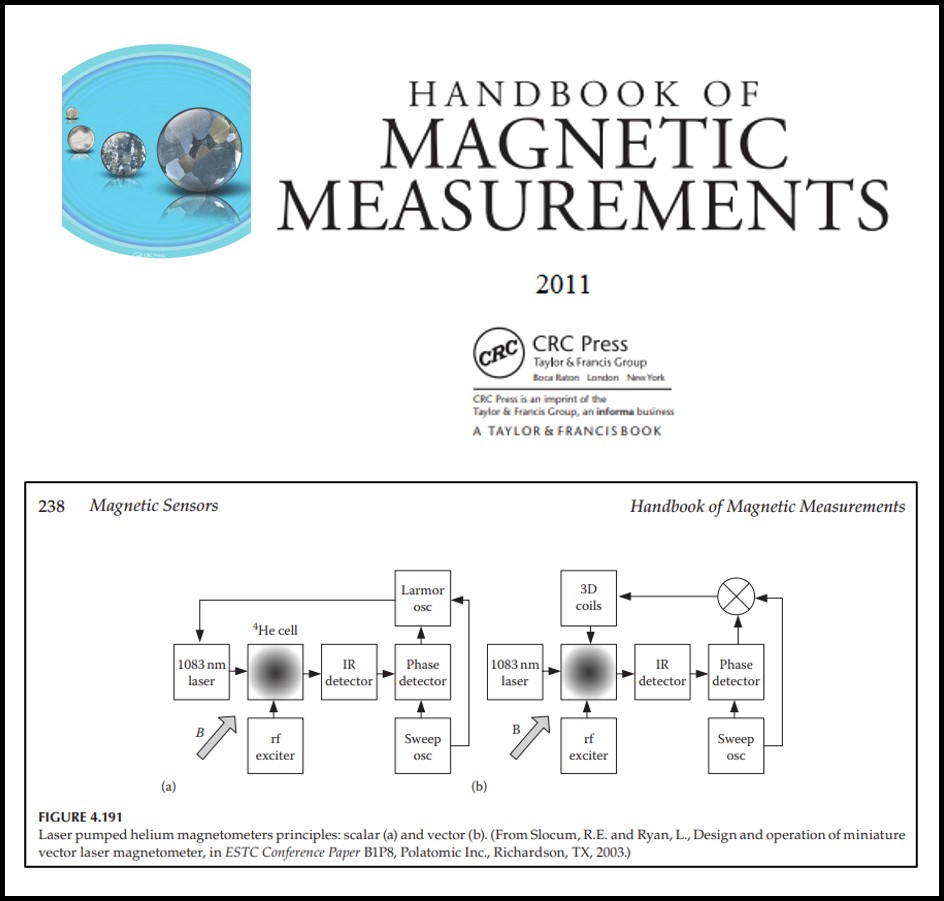
In the Magnetic Sensors chapter of the CRC Handbook of Magnetic Measurements, two helium magnetometer modes that I developed are featured. The helium is first excited by an RF exciter to the metastable 23S1 level and is then pumped by a tunable diode laser at a wavelength of 1082.91 nm. In the scalar mode, the output from the phase detector is used as a control signal to optically modulate the laser system at the Larmor frequency. In the vector mode, the output from the phase detector drives a 3D Helmholtz coil system that produces feedback currents to provide measurements of the field vector components.
Helmholtz Coil Systems
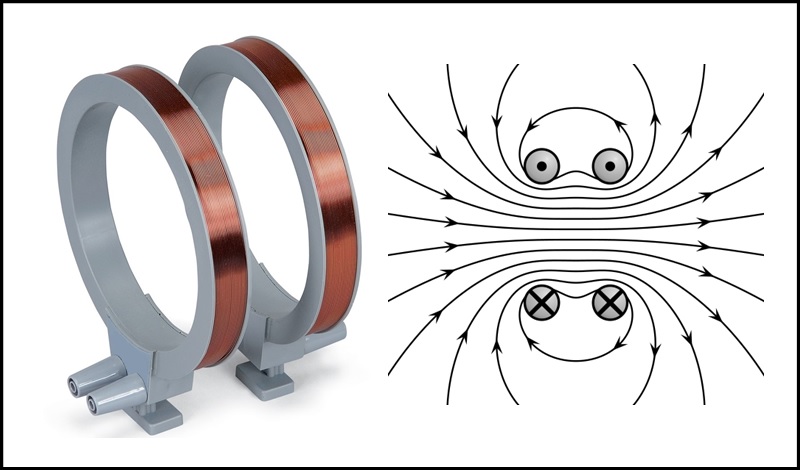
Designed multiple Helmholtz coil systems ranging in diameters from 10 cm to 75 cm. The Helmholtz coil systems consisted of two conducting circular coils, each carrying a current. The coils were separated by a distance equal to the radius of the circular loops. The magnetic field was controlled by a high current power supply circuit interfaced to a National Instruments PCI-MIO-16E-4 running LabVIEW. Single axis and triaxial coils were designed to produce a uniform field in the center of the coil system which could cancel Earth’s magnetic field. The triaxial design allowed an additional field to be injected which provided 3D orientation of a magnetic field in the center of the coil system.
Atomic Optically Pumped Magnetometer Development
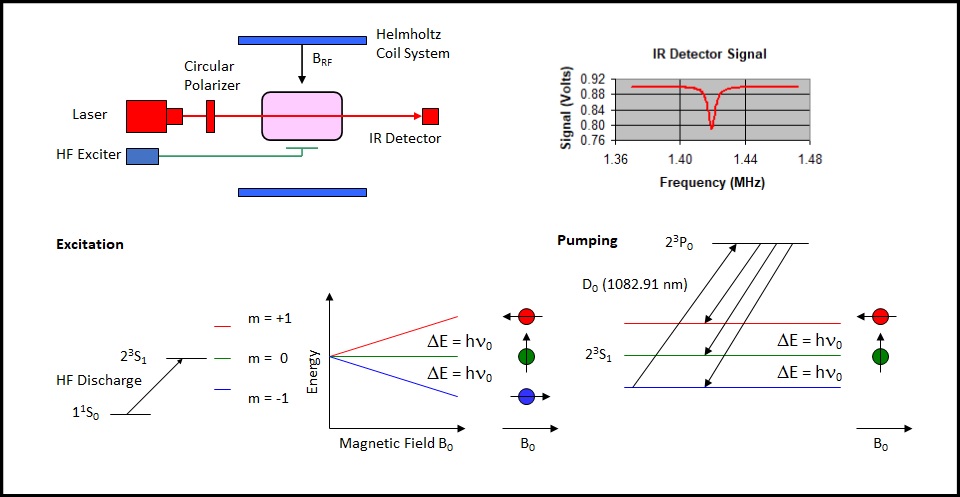
Developed atomic optically pumped magnetometer systems which use He4 gas cells as magnetic sensors. An RF source excites the helium atoms to their metastable state and a beam of circularly polarized resonance radiation passes along the axis of the magnetic field and through the cell. In a weak magnetic field, the metastable state is split into three Zeeman sublevels. The energy separation between the sublevels is directly proportional to the magnetic field. The resonance radiation of wavelength 1082.91 nm orients the magnetic moments, or populations of the triplet metastable helium atom, by the process of optical pumping. This polarization can be reset by the application of a radio frequency magnetic field at right angles to the constant magnetic field and at a frequency of f = 28 Hz/nT x B corresponding to the Zeeman splitting of the sublevels. The resonance condition can be observed because the amount of pumping light removed from the beam depends upon the population ratios (and hence on the magnitude of the magnetic moment) of the Zeeman sublevels.
Magnetic Gradiometer
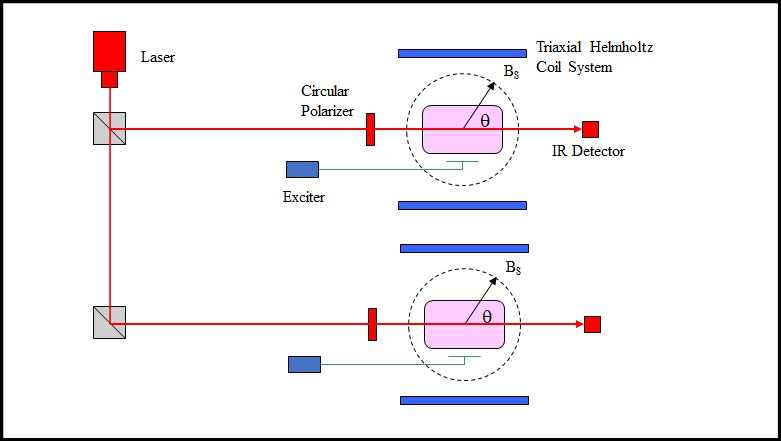
The gradiometer was built for multiple DOD military applications and consisted of a sensor unit, an electronics unit and a PC control unit. The sensor unit consisted of two laser pumped helium magnetometer sensors separated by one foot. Triaxial Helmholtz coils surrounding the cell were used to apply rotating sweep fields to modulate the absorption in the cell and carry steady feedback currents which nulled the ambient field components. The resulting feedback currents provided measurements of the field components. The gradiometer measurement was made by differencing the nulling currents for each parallel component pair in order to measure a set of three orthogonal vector gradients.
Nuclear Magnetic Resonance Magnetometer
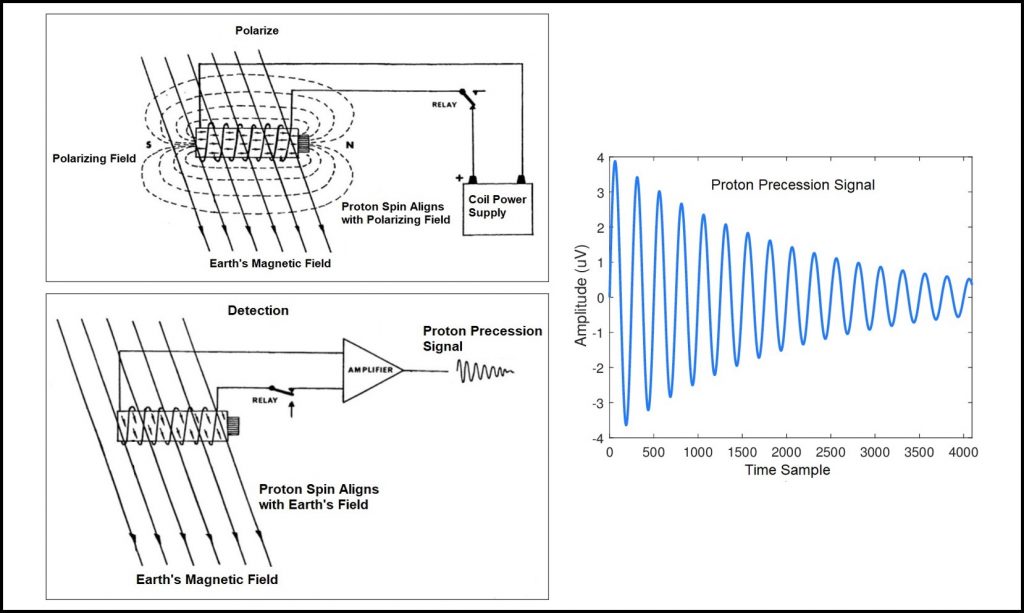
Designed and tested a magnetometer system utilizing precession of protons in a distilled water bottle (5 inches length x 2 inches diameter). Operation consists of applying a direct current to a solenoid coil surrounding the bottle which creates a strong magnetic field in the hydrogen fluid (H2O) causing the protons to align and polarize with the field. The current is then turned off and as the protons realign with the ambient magnetic field, they precess at a frequency that is directly proportional to the field strength. This produces a weak rotating magnetic field that is picked up by the coil inductor. The proton gyromagnetic ratio (0.042576 Hz/nT) defines the relationship between the frequency of the induced current and the strength of the magnetic field. The prototype system had a polarize mode and detection mode to measure slowly changing magnetic fields. Detection mode low-noise amplifier had a voltage gain of one million with a narrow bandwidth tunable audio filter.
Amorphous-Core Magnetic Sensor
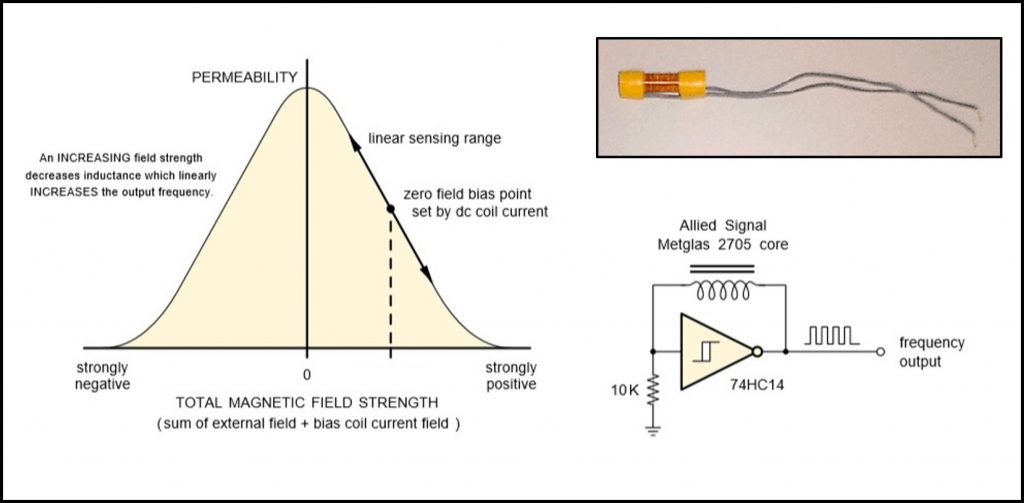
Developed magneto-inductive sensor using solid-state amorphous-core material (Metglas 2705M). The cobalt-based magnetic alloy was characterized with near-zero magnetostriction and high DC-permeability. The magnetic sensor utilized the variable permeability of the Metglas material to vary the inductance of a coil in proportion to the applied magnetic field. A Schmitt trigger relaxation RL oscillator circuit was designed to output digital pulses with frequency proportional to the field strength. The unique design operated in a different mode than a traditional fluxgate sensor since the core material never entered hard saturation.